The workforce in manufacturing in changing. Advanced manufacturing requires skilled workers, and they are in short supply across the US. Even China with its cheap labor is modernizing its plants and seeking greater numbers of skilled workers. While we often hear about the coming plant that has so much automation it needs few workers, in reality, plants are seeing a shift to skilled workers rather than a significant drawdown on the workforce.
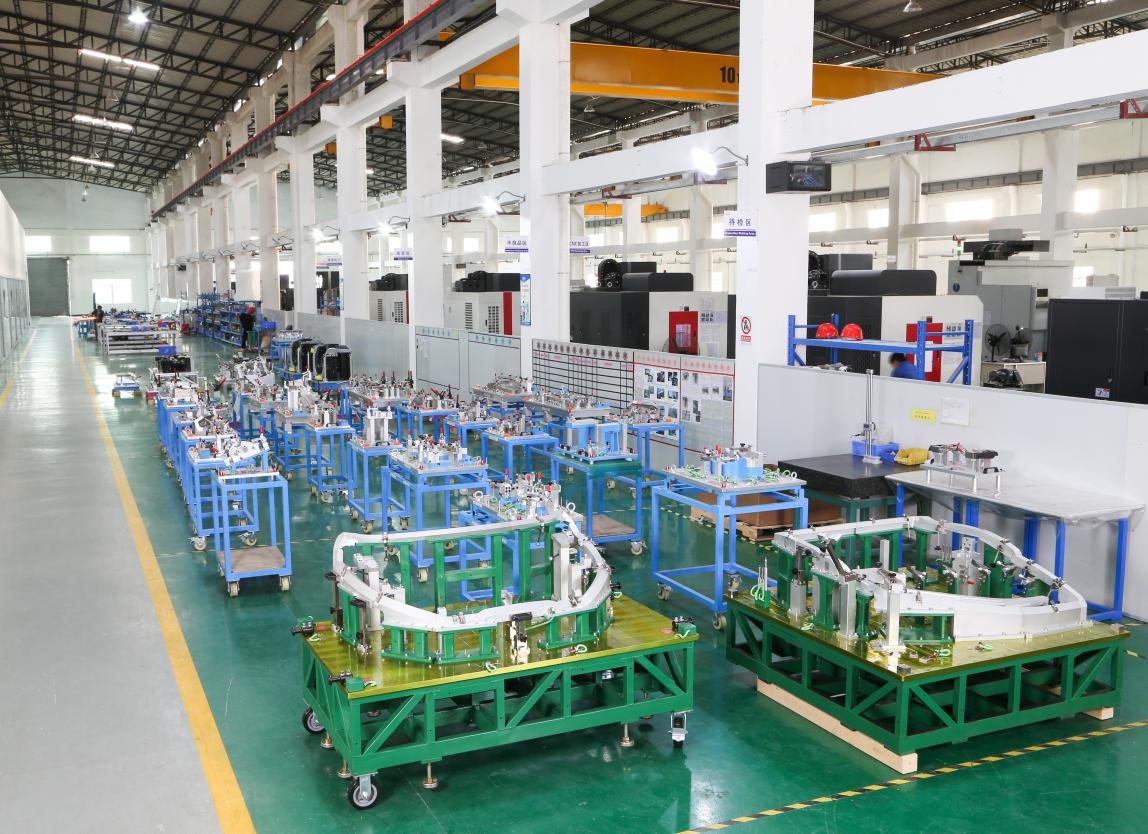
The push to bring more skilled workers into the plant has caused a gap between the need for technicians and the available workers. “The manufacturing environment is changing, and with the rapid advancement of new technology, it is becoming increasingly difficult to find workers with the skills to use it,” Nader Mowlaee, electronics engineer and career coach, told Design News. “Manufacturers need to understand that those they hire to work on the factory floor are going to be very different in the days and years ahead.”
The notion of solving this through even greater automation is many years away – though companies are working on it. “Japan claims they’re building the world’s first automated plant. We’ll see it in 2020 or 2022,” said Mowlaee. “Other countries are adopting full automation at a slower rate. In the US, we’re far away from that. It will be at least another decade before you’re going to have a robot fixing another robot.”
The Shifting Workforce
While manual labor is still needed in advanced manufacturing, the nature of that labor – and the volume of that labor – will change. “We still need both manual and technical labor. Maybe 30% of manual labor will remain, but it will be workers in white suits and gloves working with machines that are clean and solar-powered,” said Mowlaee, who will be part of the panel presentation, Workforce Integration in the New Age of Smart Manufacturing, on Tuesday, February 6, 2018, at the Pacific Design and Manufacturing show in Anaheim, Calif. “One question that comes up is what to do with the maintenance person when there are no machines breaking. You can't expect them to become a programmer. That doesn't work.”
Mowlaee is also seeing a trend toward redeploying engineers into customer-facing jobs. So many of the highest-skilled plant workers will be outside the plant with customers. “If you look at the data from LinkedIn, sales and customer service is the hot topic for engineering. For engineers, positions in sales and customer relationship rank first,” said Mowlaee. “You work with the robot and then you get on the road. Companies like Rockwell are integrating their technical people with their customer interactions.”
Filling Tech Position with Middle-Skill Workers
Solving the shortage of skilled workers for manufacturing will require creativity. One move is to grab technical people before they graduate from college. “An interesting pattern that’s emerging within the STEM industry is the increasing demand for middle-skill talent. Middle-skill jobs require more than a high school diploma, but less than a four-year degree,” Kimberly Keaton Williams, VP of technical workforce solutions and talent acquisition at Tata Technologies, told Design News. “Due to the urgent demand, many manufacturers are recruiting students mid-degree and then training them in-house.”